11 Claves para Optimizar los Gastos Indirectos de Fabricación en su Empresa
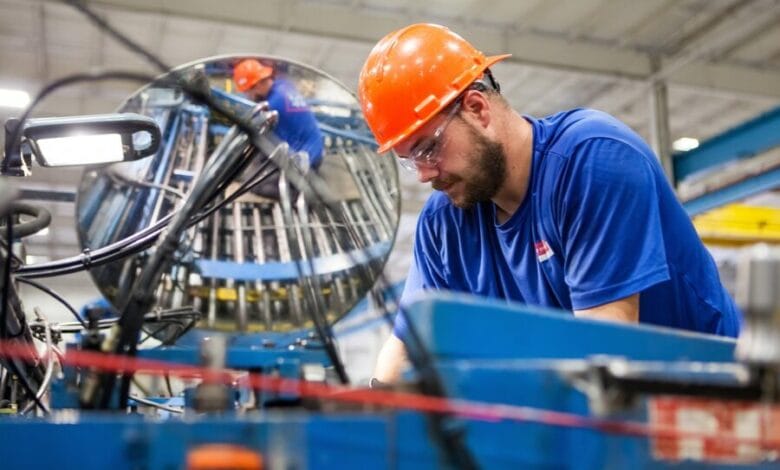
Los gastos indirectos de fabricación son aquellos costos que no están directamente relacionados con el producto final, pero son esenciales para el funcionamiento de una empresa manufacturera. Optimizar estos gastos puede tener un impacto significativo en la rentabilidad de su negocio. En este artículo, compartiremos 11 claves fundamentales para ayudarlo a gestionar eficazmente los gastos indirectos de fabricación y mejorar su línea de resultados.
Tabla de Contenidos
- 1. Gastos indirectos de fabricación: ¿Qué son y por qué importan?
- 2. Identifique y clasifique los gastos indirectos
- 3. Implemente un sistema de seguimiento de costos
- 4. Optimice el uso de la energía
- 5. Reduzca los costos de mantenimiento
- 6. Mejore la gestión del inventario
- 7. Negocie con proveedores
- 8. Optimice la planificación de la producción
- 9. Fomente una cultura de ahorro de costos
- 10. Aproveche la automatización y la tecnología
- 11. Evalúe y ajuste continuamente
- Conclusión
1. Gastos indirectos de fabricación: ¿Qué son y por qué importan?
1.1 Definición de gastos indirectos de fabricación
Los gastos indirectos de fabricación, también conocidos como costos indirectos o gastos generales de fabricación, son todos aquellos costos que no están directamente relacionados con el producto final, pero son necesarios para el funcionamiento de una empresa manufacturera. Estos gastos pueden incluir el alquiler del espacio de fabricación, la depreciación de la maquinaria, los suministros de limpieza, los salarios del personal de supervisión y más.
A diferencia de los costos directos, como las materias primas y la mano de obra directa, los gastos indirectos de fabricación no se pueden asignar fácilmente a un producto específico. Sin embargo, estos costos deben distribuirse adecuadamente entre los productos para garantizar una fijación de precios precisa y una toma de decisiones informada.
1.2 Impacto en la rentabilidad de la empresa
Los gastos indirectos de fabricación pueden representar una parte significativa de los costos totales de una empresa manufacturera. Si estos gastos no se gestionan adecuadamente, pueden erosionar los márgenes de beneficio y afectar negativamente la rentabilidad de la empresa.
Por ejemplo, si el costo de la energía utilizada en la planta de fabricación aumenta, pero no se toman medidas para optimizar el consumo de energía o negociar mejores tarifas con los proveedores, este aumento se reflejará en mayores gastos indirectos de fabricación. A su vez, esto puede llevar a un aumento en el costo total de producción y, en última instancia, a precios más altos para los clientes o márgenes de beneficio más bajos para la empresa.
Por otro lado, si una empresa logra optimizar sus gastos indirectos de fabricación, puede mejorar significativamente su rentabilidad. Al reducir los costos indirectos, la empresa puede asignar más recursos a áreas que generan ingresos, como investigación y desarrollo, marketing o expansión del negocio.
Control de calidad estadístico: conceptos básicos y aplicaciones
2. Identifique y clasifique los gastos indirectos
2.1 Categorías comunes de gastos indirectos
El primer paso para optimizar los gastos indirectos de fabricación es identificar y clasificar estos costos. Algunas categorías comunes de gastos indirectos incluyen:
- Alquiler o depreciación del espacio de fabricación
- Servicios públicos (electricidad, agua, gas)
- Mantenimiento y reparación de equipos
- Suministros de limpieza y seguridad
- Salarios del personal de supervisión y apoyo
- Seguros y impuestos relacionados con la fabricación
- Depreciación de la maquinaria y el equipo
- Costos de control de calidad
Al desglosar los gastos indirectos en categorías específicas, las empresas pueden obtener una comprensión más clara de dónde se están asignando sus recursos y identificar áreas potenciales para la optimización de costos.
2.2 Asignación de costos a centros de costos
Una vez que se han identificado las categorías de gastos indirectos, el siguiente paso es asignar estos costos a centros de costos específicos. Un centro de costos es una división o departamento dentro de una empresa a la que se pueden asignar costos con el propósito de contabilidad y presupuesto.
Por ejemplo, una empresa manufacturera puede tener centros de costos separados para ensamblaje, empaque, control de calidad y distribución. Al asignar gastos indirectos a estos centros de costos, la empresa puede obtener una comprensión más precisa de los costos asociados con cada etapa del proceso de fabricación.
Existen varios métodos para asignar gastos indirectos a centros de costos, incluyendo asignación basada en el área de piso, horas de mano de obra directa o uso de maquinaria. El método elegido dependerá de la naturaleza de los gastos indirectos y la estructura de la empresa.
3. Implemente un sistema de seguimiento de costos
3.1 Software de gestión de costos
Para optimizar eficazmente los gastos indirectos de fabricación, es esencial tener un sistema sólido para rastrear y analizar estos costos. Aquí es donde entra en juego el software de gestión de costos.
Estas herramientas permiten a las empresas capturar datos de costos de múltiples fuentes, asignar gastos indirectos a centros de costos y productos, y generar informes detallados para el análisis. Algunos ejemplos populares de software de gestión de costos incluyen SAP, Oracle y Microsoft Dynamics.
Al invertir en un sistema de gestión de costos, las empresas pueden automatizar muchas de las tareas tediosas asociadas con el seguimiento de los gastos indirectos, liberando tiempo y recursos para centrarse en iniciativas estratégicas de reducción de costos.
3.2 Monitoreo y análisis de datos regularmente
Simplemente tener un sistema de gestión de costos no es suficiente; las empresas también deben comprometerse a monitorear y analizar los datos de costos de manera regular. Esto implica generar informes de gastos indirectos de fabricación mensual o trimestralmente y comparar el rendimiento real con los presupuestos y las previsiones.
Mediante el análisis regular de los datos de costos, las empresas pueden identificar tendencias, anomalías y oportunidades de mejora. Por ejemplo, si los costos de electricidad han aumentado constantemente durante varios meses, puede ser el momento de realizar una auditoría energética o invertir en equipos más eficientes energéticamente.
El monitoreo y análisis de datos regulares también permite a las empresas responder rápidamente a los cambios en los costos y ajustar las estrategias según sea necesario. Sin este nivel de supervisión, los gastos indirectos pueden salirse fácilmente de control y erosionar los márgenes de beneficio.
4. Optimice el uso de la energía
4.1 Auditorías energéticas
Una de las áreas más significativas para optimizar los gastos indirectos de fabricación es el uso de energía. Las plantas de fabricación a menudo consumen grandes cantidades de electricidad, gas y otros recursos energéticos, lo que puede representar una parte sustancial de los costos indirectos totales.
Para identificar oportunidades de ahorro de energía, muchas empresas recurren a auditorías energéticas. Durante una auditoría energética, un profesional capacitado evaluará el uso de energía en toda la instalación, desde los sistemas de iluminación y HVAC hasta los equipos de producción y los procesos.
El auditor proporcionará un informe detallado con recomendaciones para mejorar la eficiencia energética, que pueden incluir:
- Actualización a iluminación LED
- Instalación de controles de iluminación y termostatos programables
- Optimización de los ajustes de los equipos de producción
- Reparación de fugas en sistemas de aire comprimido
- Mejora del aislamiento del edificio
Al implementar estas recomendaciones, las empresas pueden reducir significativamente su consumo de energía y los costos asociados.
4.2 Inversión en equipos eficientes
Además de hacer cambios operativos para optimizar el uso de energía, las empresas también deben considerar invertir en equipos más eficientes energéticamente. Si bien estos equipos pueden tener un costo inicial más alto, a menudo ofrecen un significativo retorno de la inversión en forma de menores costos de energía a largo plazo.
Por ejemplo, reemplazar un compresor de aire antiguo e ineficiente por un modelo nuevo y de alta eficiencia puede reducir el consumo de energía en un 20-50%. De manera similar, actualizar a motores eléctricos de alta eficiencia puede resultar en ahorros de energía del 2-10%.
Al invertir en equipos eficientes energéticamente, las empresas no solo reducen sus gastos indirectos de fabricación, sino que también demuestran su compromiso con la sostenibilidad y la responsabilidad ambiental. En una era de creciente escrutinio por parte de los consumidores y los reguladores, estos beneficios intangibles pueden ser tan valiosos como los ahorros de costos directos.
5. Reduzca los costos de mantenimiento
5.1 Mantenimiento preventivo vs reactivo
Los costos de mantenimiento y reparación de equipos pueden representar una parte significativa de los gastos indirectos de fabricación de una empresa. Para optimizar estos costos, es esencial adoptar un enfoque proactivo del mantenimiento.
Tradicionalmente, muchas empresas han confiado en el mantenimiento reactivo, que implica reparar equipos solo después de que ocurra una falla. Si bien este enfoque puede parecer ahorrar costos a corto plazo, a menudo conduce a tiempos de inactividad no planificados, menor productividad y mayores costos a largo plazo.
En cambio, las empresas deben priorizar el mantenimiento preventivo, que implica realizar inspecciones, pruebas y reparaciones programadas regularmente para evitar fallas en el equipo antes de que ocurran. Al identificar y abordar los problemas potenciales de manera proactiva, las empresas pueden:
- Reducir los tiempos de inactividad no planificados
- Extender la vida útil de los equipos
- Mejorar la eficiencia y calidad de la producción
- Reducir los costos totales de mantenimiento a largo plazo
5.2 Capacitación del personal
Otro aspecto clave de la optimización de los costos de mantenimiento es garantizar que el personal esté adecuadamente capacitado en el mantenimiento y la operación del equipo. Una capacitación adecuada puede ayudar a prevenir errores del operador que podrían conducir a daños en el equipo y tiempos de inactividad no planificados.
Además, fomentar una cultura de propiedad y responsabilidad entre los operadores de equipos puede conducir a una detección y resolución más rápida de problemas potenciales. Cuando los operadores se sienten empoderados para informar problemas y contribuir al proceso de mantenimiento, es más probable que se resuelvan los problemas antes de que se conviertan en fallas costosas.
Las empresas deben invertir en programas de capacitación regulares tanto para el personal de mantenimiento como para los operadores de equipos. Esta capacitación puede incluir:
- Prácticas recomendadas para la operación y el mantenimiento de equipos específicos
- Procedimientos de seguridad
- Solución de problemas y diagnóstico de fallas
- Uso de software de gestión del mantenimiento
Al priorizar la capacitación y el desarrollo de habilidades, las empresas pueden optimizar sus costos de mantenimiento al tiempo que mejoran la eficiencia operativa general.
6. Mejore la gestión del inventario
6.1 Método justo a tiempo (JIT)
La gestión ineficaz del inventario puede conducir a un aumento significativo en los gastos indirectos de fabricación. El exceso de inventario ata el capital, requiere espacio de almacenamiento adicional y corre el riesgo de obsolescencia. Por otro lado, el inventario insuficiente puede provocar tiempos de inactividad en la producción y pedidos pendientes de los clientes.
Para optimizar la gestión del inventario, muchas empresas han adoptado el método justo a tiempo (JIT). JIT es un enfoque de gestión de inventario en el que los materiales se adquieren y los productos se fabrican solo cuando son necesarios, en lugar de mantener grandes inventarios.
Bajo un sistema JIT, las empresas trabajan en estrecha colaboración con los proveedores para garantizar entregas frecuentes y puntuales de materiales. La producción se sincroniza con la demanda del cliente, y los productos se fabrican en lotes pequeños para minimizar el inventario de trabajo en proceso.
Al adoptar JIT, las empresas pueden:
- Reducir los costos de mantenimiento de inventario
- Liberar capital atado para otras inversiones
- Disminuir los requisitos de espacio de almacenamiento
- Mejorar el flujo de efectivo y la liquidez
- Responder más rápidamente a los cambios en la demanda del cliente
Sin embargo, implementar JIT requiere una coordinación y comunicación estrechas entre la empresa, sus proveedores y clientes. Las interrupciones en la cadena de suministro o los cambios repentinos en la demanda pueden ser más difíciles de manejar en un sistema JIT, por lo que es esencial la planificación y la gestión de riesgos adecuadas.
6.2 Análisis ABC del inventario
Otro método para optimizar la gestión del inventario es el análisis ABC. Este enfoque implica clasificar los artículos de inventario en tres categorías en función de su valor y frecuencia de uso:
- Artículos A: Estos son los artículos de alto valor que constituyen una pequeña porción del inventario total pero representan una gran parte del valor total del inventario.
- Artículos B: Estos son artículos de valor moderado que constituyen una porción moderada del inventario total y representan una parte moderada del valor total del inventario.
- Artículos C: Estos son artículos de bajo valor que constituyen una gran porción del inventario total pero representan solo una pequeña parte del valor total del inventario.
Al realizar un análisis ABC, las empresas pueden priorizar sus esfuerzos de gestión de inventario en los artículos que tienen el mayor impacto en los costos indirectos de fabricación. Por ejemplo, los artículos A pueden requerir controles de inventario más estrictos y monitoreo frecuente, mientras que los artículos C pueden gestionarse con controles menos rigurosos.
El análisis ABC también puede ayudar a las empresas a identificar oportunidades para:
- Optimizar los niveles de inventario de seguridad
- Negociar mejores términos con los proveedores de artículos de alto valor
- Reducir o eliminar el inventario de artículos obsoletos o de movimiento lento
- Mejorar la precisión del pronóstico y la planificación de la demanda
Al centrarse en los artículos de inventario que tienen el mayor impacto en los costos y la rentabilidad, las empresas pueden optimizar sus gastos indirectos de fabricación sin comprometer la calidad o la capacidad de respuesta al cliente.
7. Negocie con proveedores
7.1 Consolidación de proveedores
Una estrategia eficaz para optimizar los gastos indirectos de fabricación es negociar mejores términos y precios con los proveedores. Sin embargo, manejar múltiples proveedores puede ser un desafío, tanto desde una perspectiva logística como de costos.
La consolidación de proveedores implica reducir la cantidad total de proveedores y concentrar las compras con un grupo selecto de socios estratégicos. Al consolidar proveedores, las empresas pueden:
- Aprovechar un mayor poder de compra para negociar mejores precios
- Reducir los costos administrativos asociados con la gestión de múltiples proveedores
- Mejorar la comunicación y la colaboración con los proveedores clave
- Asegurar un suministro más confiable de materiales críticos
- Simplificar la logística y reducir los costos de transporte
Por supuesto, la consolidación de proveedores también conlleva riesgos. Depender de menos proveedores puede aumentar la vulnerabilidad a las interrupciones de la cadena de suministro si un proveedor clave experimenta dificultades. Es esencial que las empresas evalúen cuidadosamente los posibles socios proveedores y desarrollen planes de contingencia para mitigar los riesgos de la cadena de suministro.
7.2 Contratos a largo plazo
Otro enfoque para optimizar los gastos indirectos de fabricación a través de las negociaciones con proveedores es establecer contratos a largo plazo. Los contratos a largo plazo son acuerdos con proveedores que establecen términos, condiciones y precios para un período prolongado, generalmente de varios años.
Los beneficios de los contratos a largo plazo incluyen:
- Precios más bajos debido a compromisos de volumen a largo plazo
- Menor volatilidad de precios y protección contra aumentos de precios del mercado
- Suministro garantizado de materiales críticos
- Planificación y previsión mejoradas debido a compromisos de pedidos a futuro
- Oportunidades para colaboración e innovación con proveedores
Sin embargo, los contratos a largo plazo también pueden tener desventajas. Las empresas pueden quedar encerradas en términos desfavorables si las condiciones del mercado cambian o si surgen nuevas tecnologías. Además, los contratos a largo plazo pueden reducir la flexibilidad para cambiar proveedores si el desempeño se deteriora o surgen mejores alternativas.
Para mitigar estos riesgos, las empresas deben incorporar cuidadosamente cláusulas de escape y disposiciones de renegociación en los contratos a largo plazo. También es crucial asociarse con proveedores que tengan un historial comprobado de confiabilidad, calidad e innovación.
Al adoptar un enfoque estratégico de las negociaciones con proveedores, que incluye la consolidación de proveedores y los contratos a largo plazo, las empresas pueden optimizar significativamente sus gastos indirectos de fabricación y construir una cadena de suministro más resistente y rentable.
8. Optimice la planificación de la producción
8.1 Programación de la producción
Un aspecto clave de la optimización de los gastos indirectos de fabricación es la planificación eficaz de la producción. La programación ineficiente de la producción puede dar lugar a tiempos de inactividad, cuellos de botella y exceso de inventario, todo lo cual contribuye a mayores costos indirectos.
Para optimizar la programación de la producción, las empresas deben adoptar un enfoque sistemático que tenga en cuenta factores como:
- Previsión de la demanda: Utilizar técnicas de pronóstico precisas para predecir la demanda futura de los clientes y alinear los planes de producción en consecuencia.
- Capacidad de producción: Comprender las limitaciones de capacidad de los equipos, la mano de obra y las instalaciones, y programar la producción para maximizar la utilización sin causar cuellos de botella.
- Tiempos de configuración: Minimizar los tiempos de configuración y cambio entre productos para reducir los tiempos de inactividad y mejorar la flexibilidad de la producción.
- Mantenimiento: Coordinar los horarios de producción con los planes de mantenimiento preventivo para evitar interrupciones no planificadas.
- Niveles de inventario: Monitorear los niveles de inventario de materias primas, trabajo en proceso y productos terminados, y ajustar los programas de producción para optimizar el flujo de materiales y minimizar el inventario estancado.
Existen varias herramientas y técnicas que las empresas pueden emplear para optimizar la programación de la producción, que incluyen:
- Planificación de requerimientos de materiales (MRP): Un sistema para planificar y programar la producción basado en la demanda dependiente de los artículos de nivel superior.
- Programación de capacidad finita (FCS): Un enfoque que tiene en cuenta las limitaciones de capacidad de los recursos al generar programas de producción viables.
- Teoría de restricciones (TOC): Una metodología que se centra en identificar y explotar el recurso más limitado o «restricción» en un sistema de producción.
Al invertir en herramientas y procesos avanzados de planificación de la producción, las empresas pueden optimizar su flujo de producción, reducir los gastos indirectos y mejorar la capacidad de respuesta al cliente.
8.2 Reducción de tiempos de preparación
Otro aspecto importante de la optimización de la planificación de la producción es la reducción de los tiempos de preparación. El tiempo de preparación se refiere al tiempo necesario para cambiar una línea de producción de un producto a otro. Durante un cambio, la producción debe detenerse, lo que resulta en tiempos de inactividad y menor productividad.
Para minimizar los tiempos de preparación, las empresas pueden emplear varias estrategias, que incluyen:
- Metodología SMED (Single-Minute Exchange of Dies): Una técnica desarrollada por Shigeo Shingo que se enfoca en reducir sistemáticamente los tiempos de cambio a través de la externalización, simplificación y racionalización de las actividades de preparación.
- Diseño de producto modular: Diseñar productos con componentes y subensamblajes estandarizados que permitan cambios más rápidos y sencillos entre variantes de productos.
- Plantillas y accesorios de cambio rápido: Invertir en plantillas, sujetadores y otros accesorios que faciliten el cambio rápido de matrices, herramientas y equipos.
- Preparación fuera de línea: Realizar tantas actividades de preparación como sea posible «fuera de línea» o mientras el equipo aún está funcionando, para minimizar el tiempo de inactividad durante los cambios reales.
- Capacitación del operador: Capacitar a los operadores en técnicas de cambio eficientes y establecer metas claras para los tiempos de cambio.
Al reducir los tiempos de preparación, las empresas pueden mejorar la flexibilidad de la producción, reducir el tamaño de los lotes y minimizar el inventario de trabajo en proceso. Esto, a su vez, conduce a menores gastos indirectos de fabricación, tiempos de entrega más rápidos y mayor capacidad de respuesta a los cambios en la demanda de los clientes.
La optimización de la planificación de la producción, que incluye la programación eficaz de la producción y la reducción de los tiempos de preparación, es un componente crucial de cualquier estrategia para racionalizar los gastos indirectos de fabricación y mejorar el rendimiento operativo general.
9. Fomente una cultura de ahorro de costos
9.1 Participación de los empleados
Para optimizar de manera sostenible los gastos indirectos de fabricación, las empresas deben ir más allá de las iniciativas impulsadas por la gerencia y fomentar una cultura de ahorro de costos en toda la organización. Uno de los elementos clave de esta cultura es la participación activa de los empleados en los esfuerzos de reducción de costos.
Los empleados de primera línea a menudo tienen el conocimiento más íntimo de los procesos de producción y son los primeros en identificar oportunidades de mejora. Al involucrar activamente a estos empleados y solicitar sus ideas y comentarios, las empresas pueden aprovechar un valioso grupo de conocimientos para optimizar los gastos indirectos.
Algunas estrategias para fomentar la participación de los empleados incluyen:
- Programas de sugerencias: Establecer un programa formal para que los empleados envíen ideas de ahorro de costos y mejoras de procesos, con un proceso claro para evaluar e implementar sugerencias viables.
- Equipos de mejora continua: Formar equipos multifuncionales de empleados para identificar y abordar oportunidades de reducción de costos en áreas específicas, como energía, mantenimiento o gestión de inventario.
- Capacitación en Lean Manufacturing: Brindar capacitación a los empleados sobre los principios y herramientas de Lean Manufacturing, como 5S, Kaizen y mapeo de flujo de valor, para que puedan identificar y eliminar desperdicios en sus áreas de trabajo.
- Comunicación abierta: Fomentar un entorno en el que los empleados se sientan cómodos compartiendo ideas y preocupaciones relacionadas con los costos, y brindar retroalimentación regular sobre el progreso de las iniciativas de reducción de costos.
Al empoderar a los empleados para que participen activamente en los esfuerzos de ahorro de costos, las empresas no solo pueden aprovechar una valiosa fuente de ideas, sino que también pueden fomentar un mayor sentido de propiedad y responsabilidad en toda la organización.
9.2 Incentivos y reconocimiento
Otro componente crítico de la creación de una cultura de ahorro de costos es proporcionar incentivos y reconocimiento apropiados para los empleados que contribuyen a los esfuerzos de reducción de costos. Al alinear los incentivos de los empleados con los objetivos de ahorro de costos de la empresa, las organizaciones pueden impulsar un cambio de comportamiento duradero y sostenible.
Algunos enfoques para incentivar y reconocer el ahorro de costos incluyen:
- Bonos de ahorro de costos: Ofrecer bonos u otros incentivos financieros a los empleados o equipos que logren o superen los objetivos específicos de reducción de costos.
- Reconocimiento público: Celebrar públicamente los logros de ahorro de costos de los empleados a través de boletines internos, eventos de reconocimiento o premios de la compañía.
- Avance profesional: Considerar los logros de ahorro de costos en las decisiones de promoción y avance profesional, demostrando que la contribución a la rentabilidad de la empresa es valorada y recompensada.
- Participación en las ganancias: Implementar un programa de participación en las ganancias que recompense a todos los empleados cuando la empresa logre o supere los objetivos generales de rentabilidad y eficiencia.
Es importante que los incentivos y el reconocimiento estén respaldados por métricas claras y objetivas, para garantizar que los esfuerzos de ahorro de costos estén alineados con los objetivos comerciales más amplios y no tengan consecuencias no deseadas. Por ejemplo, las reducciones de costos no deben comprometer la calidad del producto, la seguridad de los empleados o la satisfacción del cliente.
Al fomentar una cultura de ahorro de costos que valore la participación, la innovación y la propiedad de los empleados, las empresas pueden generar un impulso poderoso y sostenible para optimizar los gastos indirectos de fabricación. Esta cultura no solo ayudará a impulsar la rentabilidad a corto plazo, sino que también posicionará a la empresa para el éxito a largo plazo al inculcar un enfoque continuo en la eficiencia y la mejora continua.
10. Aproveche la automatización y la tecnología
10.1 Robótica y automatización de procesos
En el entorno de fabricación actual, la automatización y la tecnología desempeñan un papel cada vez más importante en la optimización de los gastos indirectos de fabricación. Una de las tecnologías más transformadoras en este sentido es la robótica y la automatización de procesos.
Los robots industriales y los sistemas de automatización pueden realizar una amplia gama de tareas, desde soldadura y pintura hasta ensamblaje y empaque, a menudo con mayor velocidad, precisión y consistencia que los trabajadores humanos. Al automatizar procesos que anteriormente eran intensivos en mano de obra, las empresas pueden:
- Reducir los costos laborales directos e indirectos
- Mejorar la calidad y reducir los errores y el reproceso.
- Aumentar el rendimiento y reducir los tiempos de ciclo
- Mejorar la seguridad de los empleados al eliminar tareas peligrosas o repetitivas
- Optimizar el uso del espacio en la planta al reducir la necesidad de estaciones de trabajo manual
Por supuesto, implementar soluciones robóticas y de automatización requiere una inversión inicial significativa, tanto en términos de capital como de desarrollo de habilidades de la fuerza laboral. Las empresas deben evaluar cuidadosamente el retorno de la inversión y desarrollar un plan claro para integrar estas tecnologías en sus operaciones existentes.
10.2 Análisis de datos y aprendizaje automático
Otra área clave donde la tecnología puede ayudar a optimizar los gastos indirectos de fabricación es en el análisis de datos y el aprendizaje automático. Con el advenimiento de la Internet de las cosas (IoT) y los sensores inteligentes, las empresas manufactureras ahora tienen acceso a vastas cantidades de datos sobre sus operaciones, desde el rendimiento de los equipos y el consumo de energía hasta la calidad del producto y los tiempos de entrega.
Al aprovechar herramientas avanzadas de análisis y algoritmos de aprendizaje automático, las empresas pueden convertir estos datos en información procesable para impulsar la toma de decisiones y la optimización de costos. Algunos ejemplos incluyen:
- Mantenimiento predictivo: Analizar los datos de los sensores de los equipos para predecir cuándo es probable que ocurran fallas, permitiendo un mantenimiento más específico y reduciendo los costosos tiempos de inactividad no planificados.
- Optimización del consumo de energía: Utilizar datos en tiempo real sobre el uso de energía para identificar ineficiencias, optimizar la programación de la producción y minimizar los costos de energía.
- Control de calidad impulsado por datos: Aplicar algoritmos de aprendizaje automático a los datos de inspección y prueba para identificar de manera más efectiva productos defectuosos, reducir las tasas de falsos positivos y prevenir costosos retiros de productos.
- Optimización de inventario: Utilizar técnicas avanzadas de pronóstico y optimización para mejorar la precisión de la planificación de inventario, reducir el inventario de seguridad y minimizar la obsolescencia.
Para aprovechar al máximo el análisis de datos y el aprendizaje automático, las empresas deben invertir en la infraestructura tecnológica adecuada, así como en el talento y las habilidades necesarias para interpretar y actuar sobre los conocimientos generados por estas herramientas. Esto puede requerir asociaciones con proveedores externos o el desarrollo de capacidades internas de ciencia de datos.
Al aprovechar el poder de la automatización, la robótica, el análisis de datos y el aprendizaje automático, las empresas manufactureras pueden desbloquear nuevas eficiencias, reducir los costos y mejorar su agilidad y capacidad de respuesta en un entorno empresarial cada vez más dinámico y competitivo. Si bien la adopción de estas tecnologías puede ser desafiante, los beneficios potenciales para la optimización de los gastos indirectos de fabricación son significativos y de gran alcance.
11. Evalúe y ajuste continuamente
11.1 Revisiones periódicas de costos
La optimización de los gastos indirectos de fabricación no es un esfuerzo único, sino un proceso continuo que requiere monitoreo, evaluación y ajuste regulares. Para mantener el impulso y garantizar la alineación continua con los objetivos empresariales más amplios, las empresas deben realizar revisiones periódicas de los costos.
Estas revisiones deben llevarse a cabo al menos trimestralmente e involucrar a las partes interesadas clave de las funciones de finanzas, operaciones y cadena de suministro. El objetivo es evaluar el desempeño en relación con los KPI y objetivos de costos establecidos, identificar áreas de mejora y hacer ajustes a las estrategias e iniciativas según sea necesario.
Algunos puntos clave a considerar durante las revisiones de costos incluyen:
- Variaciones de los gastos reales frente al presupuesto en categorías de costos indirectos clave
- Tendencias y anomalías en el consumo de energía, gastos de mantenimiento, costos de inventario, etc.
- Progreso en iniciativas específicas de reducción de costos y logro de hitos
- Cambios en los factores externos, como los precios de las materias primas, las regulaciones o las condiciones del mercado, que pueden afectar los costos indirectos
- Oportunidades para aumentar o reducir los esfuerzos en función del retorno de la inversión y el impacto empresarial
Los hallazgos y las decisiones de las revisiones de costos deben documentarse y comunicarse claramente a los equipos relevantes, con un plan de acción claro y responsabilidades asignadas para abordar cualquier problema o impulsar mejoras específicas.
11.2 Mejora continua de procesos
Además de las revisiones periódicas de costos, las empresas también deben adoptar un enfoque de mejora continua de procesos para optimizar los gastos indirectos de fabricación. La mejora continua es una filosofía que busca mejorar incrementalmente los procesos a lo largo del tiempo, en lugar de depender únicamente de iniciativas de transformación a gran escala.
En el contexto de los gastos indirectos de fabricación, la mejora continua puede tomar muchas formas, como:
- Eventos Kaizen: Proyectos enfocados a corto plazo que reúnen a equipos interfuncionales para abordar rápidamente un desafío específico de reducción de costos o eficiencia.
- Análisis de causa raíz: Investigar y abordar de manera sistemática las causas fundamentales de los problemas de costos, en lugar de simplemente tratar los síntomas superficiales.
- Estudios de benchmarking: Comparar el desempeño de costos y las mejores prácticas con empresas pares y líderes de la industria para identificar oportunidades de mejora.
- Entrenamiento y desarrollo de habilidades: Invertir en la capacitación continua de los empleados en metodologías de reducción de costos y herramientas de mejora de procesos como Lean Six Sigma.
- Desarrollo de proveedores: Trabajar en colaboración con proveedores clave para identificar oportunidades de reducción de costos, mejorar la eficiencia y promover la innovación en toda la cadena de suministro.
Para sostener una cultura de mejora continua, es fundamental que los líderes demuestren un compromiso visible con el proceso, comuniquen regularmente el progreso y el éxito, y empoderen a los empleados a todos los niveles para identificar e implementar mejoras.
Al combinar revisiones periódicas estructuradas de costos con un compromiso continuo con la mejora incremental, las empresas pueden mantener su enfoque en optimizar los gastos indirectos de fabricación y conducir un valor significativo y duradero para el negocio. Este enfoque de dos frentes no solo ayuda a capturar las eficiencias a corto plazo, sino que también posiciona a la empresa para una competitividad y rentabilidad a largo plazo en un panorama manufacturero en constante evolución.
Conclusión
Optimizar los gastos indirectos de fabricación es un imperativo estratégico para las empresas manufactureras que buscan mantenerse competitivas en el entorno empresarial actual. Al adoptar un enfoque integral que abarque la identificación y clasificación de costos, la implementación de sistemas de gestión, la optimización del uso de energía, la reducción de los costos de mantenimiento, la mejora de la gestión del inventario, la negociación con proveedores, la optimización de la planificación de la producción, el fomento de una cultura de ahorro de costos, el aprovechamiento de la automatización y la tecnología, y la evaluación y ajuste continuos, las empresas pueden desbloquear eficiencias significativas y mejorar su línea de resultados.
Sin embargo, es importante recordar que la optimización de los gastos indirectos de fabricación no es una propuesta única, sino un viaje continuo que requiere un compromiso sostenido, inversión y apoyo de toda la organización. Requiere un liderazgo visionario, una toma de decisiones basada en datos, una comunicación clara y una mentalidad de mejora continua en todos los niveles.
Al aceptar este desafío y adoptar las estrategias y mejores prácticas descritas en este artículo, las empresas manufactureras pueden posicionarse para un éxito duradero, no solo en términos de reducción de costos, sino también en términos de agilidad, innovación y satisfacción del cliente. En última instancia, la capacidad de optimizar eficazmente los gastos indirectos de fabricación no es solo una ventaja competitiva, sino un requisito fundamental para prosperar en el panorama manufacturero dinámico y en constante cambio de hoy.